신타비아(SINTAVIA)는 항공우주 & 국방, 오일 & 천연 가스, 자동차, 지상 발전과 같은 주요 산업에 대한 금속 적층 제조(AM)를 지원하는, 이 분야의 글로벌 리더 기업입니다. 이 회사는 각 산업의 까다로운 기준을 충족하는 금속 부품들의 파라미터 최적화 및 고품질 모델 생산을 위해 힘쓰고 있습니다.
세계 어디를 찾아봐도 다른 독립적인 AM 회사들이 신타비아와 같이 자체적인 기능들을 보유하고 있지는 않습니다. 신타비아는 6개의 최고 사양의 프린터를 이용하여, 세계적인 글로벌 OEM 4곳과 열간 등압 성형, 진공 열처리, 산업용 CT 스캐너, 와이어 EDM, 고온 인장 강도와 피로 그리고 크립 테스트를 포함한 기계 시험 장비, 스캐닝 전자 현미경과 광 방출 분광기가 포함된 실험실, 정밀 입자 실험실 등에 대한 협업으로 다른 경쟁사들보다 훨씬 빠르게 파라미터를 최적화하고, 직접 제조하며, 품질 검사도 수행하고 있습니다.
신타비아의 사장인 더그 햇지스(Doug Hedges)는 기계 엔지니어이자 적층 제조의 전문가입니다. 그는 부품 제조 승인(PMA), 지정된 공학 대표(DER) 수리자, OEM 부품 제조 및 설계, 대규모 제트 엔진의 유지 관리, 수리, 정비(MRO) 등의 다양한 경험을 가지고 있습니다.
더그는 최근 항공우주 부품까지도 적층 제조 방식으로 생산할 수 있는 방법을 선보였습니다. 더그의 목표는 부품의 전체 중량을 줄이면서 기존 브래킷의 기계적 특성을 충족시키도록, 항공기 브래킷의 최적화 된 설계를 만드는 것이었습니다. 이를 위해 더그는 우선 이전의 경험들을 토대로 컴포넌트를 구성하기 시작했습니다. 더그는 저압 터빈 용 항공기 부품으로 쓰이는 컴포넌트를 선택했습니다. 이 파트는 각 엔진에서 총 12번이 사용되는 파트입니다.
더그는, “제 목표는 생산적인 설계와 적층 제조를 이용하여 제품의 유지 보수, 수정, 정비를 간소화하는 것입니다. 조직에서 이러한 기술을 채택하면, (내부) 제작의 간소화, 쉬운 구매, 가상 재고 관리, 폐기 혹은 중단된 부품 교체, 부품의 성능 향상 등 많은 장점을 얻을 수 있어 중량 절감, 강도 증가, 피로 특성 향상 등의 효과를 얻을 수 있을 것입니다.” 라고 설명합니다.
솔리드씽킹 인스파이어를 이용한 최적 설계
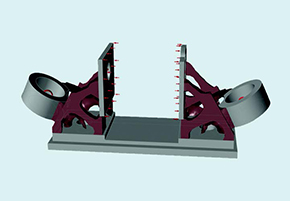
▲ 인스파이어에서 브래킷의 하중과
설계 영역을 설정
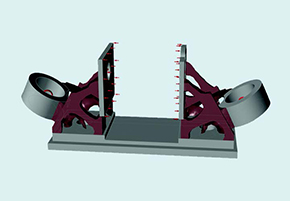
▲ 인스파이어의 최적화 결과
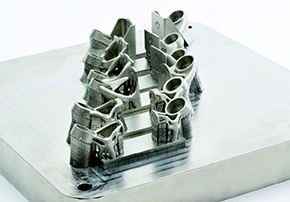
▲ SLM 280 트윈 레이저로 파트의 최종 출력
더그는 초기 컨셉에 대한 증명을 위해 신타비아가 현장에서 설계하고 제작하는 많은 도구들을 활용했습니다. 이 과정의 첫 번째 단계는 파란 광선 스캐너를 사용하여 원래 파트의 형상을 찾는 것이었습니다. 확인이 완료된 후, 더그와 그의 팀은 원래 형상의 정확한 스펙에 맞게 고충실도의 CAD 모델을 만들었습니다. 더그는, “다음으로 우리는 부품과 모든 하중 조건들을 결정했습니다. 솔리드씽킹 인스파이어(solidThinking INSPIRE)를 사용하여 이러한 조건을 모델에 적용하고, 설계가 될 공간과 고정할 설계 공간으로 분리한 후, 해당 파트에 대해 최적화 작업을 반복 실행했습니다. 여기에는 수정된 설계 공간, 다양한 압축 시험, 실제 제조 등 여러 가지를 고려하였습니다. 그 결과를 바탕으로 유한 요소 해석(Finite Element Analysis)를 실행하여 최적화한 결과를 비교하고 결정했습니다.” 라고 업무 과정을 설명했습니다. 이어서 더그와 팀은 솔리드씽킹 이볼브(solidThinking EVOVLE)의 폴리넙스(PolyNURBS) 도구를 사용하여 최종 지오메트리로 최적화를 완성했습니다.
최종 최적화 형상을 완성한 후, 신타비아는 SLM Systems의 280 트윈 레이저 기계를 사용하여, Inconel 718 파우더와 결합하여 부품을 생산했습니다. 제조의 후처리 작업도 테스트 및 준비가 완료되었습니다. 먼저 신타비아는 부품에 자체 진공 열처리를 수행한 후 EDM(방전 가공)을 사용하여 파트를 빌드 플레이트에서 제거했습니다. 그 후 제거 기법, 샌드 블라스팅 및 세련, 열간 정수압 소결법을 사용하여 파트의 빈 틈과 갈라진 부분을 제거했습니다.
신타비아는 이후 5000lbs의 하중, 피로도 테스트, 금속 시험 등을 포함한 검증 시험을 다양하게 실시했습니다. 최종 제작물은 모든 테스트에서 기존의 파트보다 성능이 뛰어났습니다. 새로운 파트는 기존보다 피로 수명이 3배나 좋았고, 다공성은 줄어들었습니다. 무게는 15% 가벼워졌습니다.
엔진 터빈도 인스파이어로!
신타비아는 적층 제조를 위한 최적화 작업은 물론, 이 파트에 대한 최적화 작업을 추가로 계획하고 있습니다. 더그는, “인스파이어를 사용하여, 엔진 터빈 파트의 질량도 더욱 줄이기 위해 계속해서 노력하고 싶습니다. 또한 카라(collar)를 강화하고, 일체형 베어링의 설계에서도 잘 작동하도록 만들 계획입니다.” 라고 앞으로의 계획을 밝혔습니다.
* 산업
– 모델 적층 제조
* 과제
– 중량을 줄이면서 기존보다 성능이 뛰어난, 최적화 된 항공 우주 부품 생산
* 알테어 솔루션
– 인스파이어를 통한 컨셉 생성과, 향상된 성능 및 무게 절감한 주문형 교체 브래킷 생산을 위해 첨단 SLM 280 사용
* 이점
• 15% 중량 감소
• 기존보다 적어진 다공성
• 피로 수명 3배 증가